Destylator przemysłowy jest kluczowym urządzeniem wykorzystywanym w przemyśle chemicznym do separacji składników mieszanin cieczy na podstawie różnic w ich temperaturach wrzenia. Proces ten polega na podgrzewaniu cieczy do momentu, gdy jeden z jej składników zaczyna parować, a następnie skraplaniu powstałej pary w celu uzyskania czystszej frakcji. W przemyśle chemicznym destylatory są używane do produkcji różnych substancji, takich jak alkohole, oleje eteryczne czy rozpuszczalniki. W zależności od zastosowania, destylatory mogą mieć różne konstrukcje, takie jak destylatory prostokątne, kolumnowe czy wirujące. Każdy z tych typów ma swoje unikalne cechy i zalety, które sprawiają, że są one dostosowane do konkretnych procesów produkcyjnych. Warto również zauważyć, że efektywność procesu destylacji może być znacznie zwiększona poprzez zastosowanie odpowiednich katalizatorów oraz optymalizację warunków operacyjnych, takich jak temperatura i ciśnienie.
Jakie są główne rodzaje destylatorów przemysłowych
W przemyśle istnieje kilka głównych typów destylatorów przemysłowych, które różnią się między sobą konstrukcją oraz zastosowaniem. Najpopularniejsze z nich to destylatory kolumnowe, które są wykorzystywane w dużych zakładach produkcyjnych do separacji wielu składników jednocześnie. W tego rodzaju urządzeniach ciecz przepływa przez kolumnę, gdzie zachodzi wielokrotna kondensacja i parowanie, co pozwala na uzyskanie wysokiej czystości frakcji. Innym rodzajem są destylatory prostokątne, które charakteryzują się prostszą budową i są często stosowane w mniejszych zakładach lub laboratoriach. Dodatkowo wyróżniamy destylatory wirujące, które dzięki swojej dynamicznej konstrukcji umożliwiają szybszą separację składników. Warto także wspomnieć o destylatorach próżniowych, które działają w obniżonym ciśnieniu, co pozwala na destylację substancji o wysokich temperaturach wrzenia bez ryzyka ich rozkładu.
Jakie są zastosowania destylatorów przemysłowych w różnych branżach
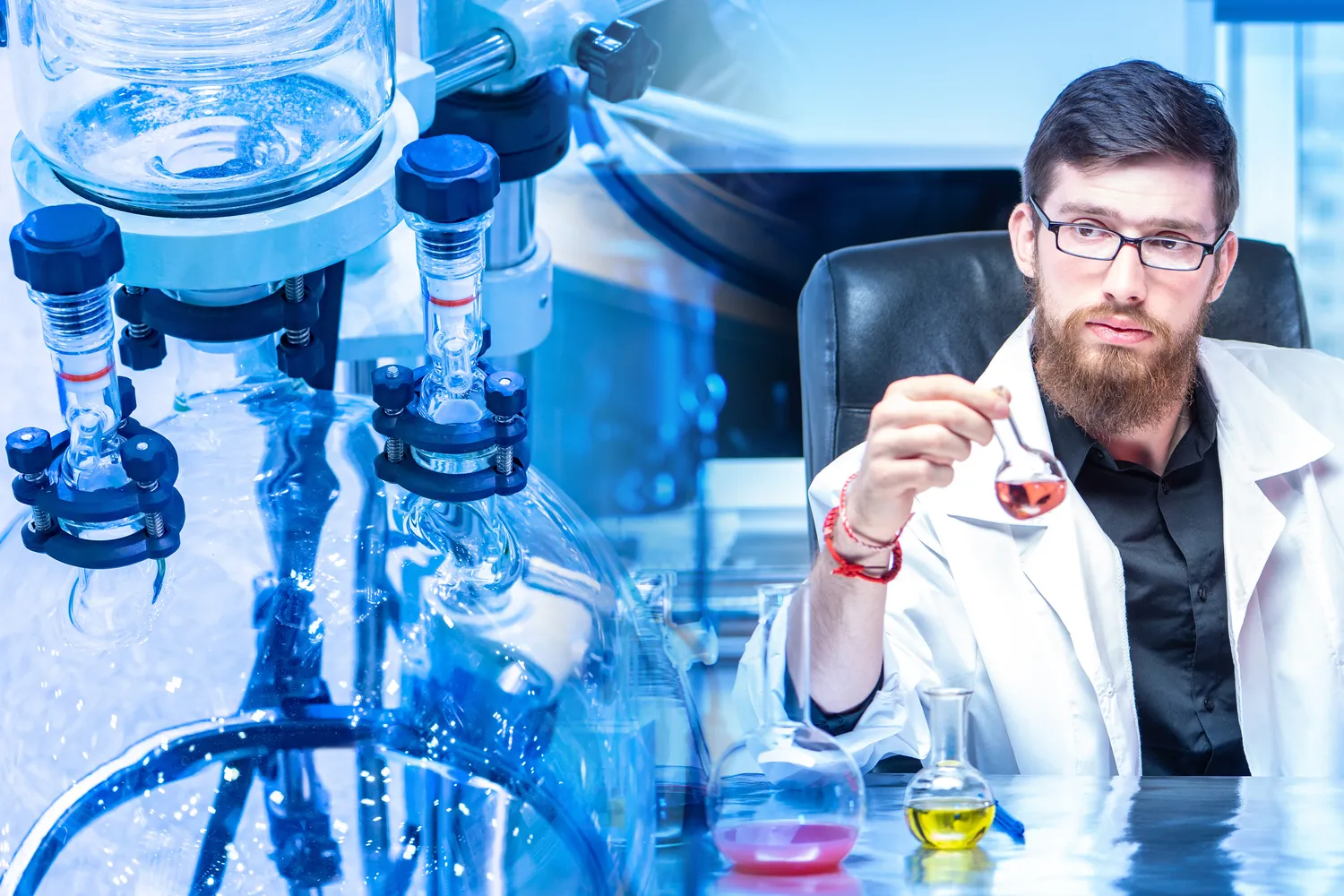
Destylatory przemysłowe znajdują szerokie zastosowanie w różnych branżach, od chemii po farmację i przemysł spożywczy. W przemyśle chemicznym służą do produkcji różnych substancji chemicznych, takich jak alkohole czy kwasy organiczne. W farmacji wykorzystuje się je do oczyszczania substancji czynnych oraz produkcji leków, gdzie wysoka czystość jest kluczowa dla skuteczności terapeutycznej. W branży spożywczej destylatory są niezbędne do produkcji napojów alkoholowych, takich jak whisky czy wódka, a także do ekstrakcji olejków eterycznych z roślin. Ponadto w przemyśle petrochemicznym stosuje się je do rafinacji ropy naftowej oraz separacji różnych frakcji paliwowych. Inne zastosowania obejmują produkcję biopaliw oraz oczyszczanie wody poprzez usuwanie zanieczyszczeń organicznych.
Jakie są najważniejsze czynniki wpływające na wydajność destylatora przemysłowego
Wydajność destylatora przemysłowego zależy od wielu czynników, które mogą znacząco wpłynąć na efektywność procesu separacji składników. Kluczowym elementem jest temperatura podgrzewania cieczy oraz ciśnienie panujące w systemie. Zbyt niska temperatura może prowadzić do niepełnej separacji składników, podczas gdy zbyt wysoka może powodować ich rozkład lub niepożądane reakcje chemiczne. Kolejnym istotnym czynnikiem jest czas kontaktu cieczy z powierzchnią chłodzącą, który powinien być odpowiednio dostosowany do rodzaju przetwarzanych substancji. Również konstrukcja samego urządzenia ma ogromne znaczenie; kolumny o odpowiedniej liczbie teoretycznych płyt mogą znacznie zwiększyć efektywność procesu poprzez umożliwienie wielokrotnego parowania i kondensacji. Dodatkowo jakość surowców oraz ich skład chemiczny również wpływają na wydajność destylacji; obecność zanieczyszczeń może prowadzić do tworzenia niepożądanych produktów ubocznych lub obniżać czystość końcowego produktu.
Jakie są najczęstsze problemy związane z destylatorami przemysłowymi
Podczas eksploatacji destylatorów przemysłowych mogą wystąpić różne problemy, które wpływają na ich wydajność i jakość uzyskiwanych produktów. Jednym z najczęstszych problemów jest tzw. „flooding”, czyli zalanie kolumny, co prowadzi do zmniejszenia efektywności separacji. Flooding może być spowodowane zbyt dużym przepływem cieczy lub niewłaściwym ustawieniem parametrów pracy urządzenia. Innym istotnym problemem jest „weeping”, które polega na niepożądanym przepływie cieczy przez otwory w kolumnie, co również wpływa na obniżenie wydajności. Dodatkowo, osady i zanieczyszczenia mogą gromadzić się w destylatorze, co prowadzi do zmniejszenia efektywności procesu oraz wymaga regularnego czyszczenia i konserwacji urządzenia. Warto również zwrócić uwagę na problemy związane z kontrolą temperatury i ciśnienia; ich niewłaściwe ustawienie może prowadzić do niepełnej separacji składników lub powstawania niepożądanych produktów ubocznych.
Jakie są nowoczesne technologie w destylacji przemysłowej
W ostatnich latach w dziedzinie destylacji przemysłowej nastąpił znaczny postęp technologiczny, który przyczynił się do zwiększenia efektywności procesów oraz poprawy jakości produktów. Jedną z nowoczesnych technologii jest zastosowanie destylacji membranowej, która pozwala na separację składników bez potrzeby podgrzewania cieczy. Dzięki temu proces ten jest bardziej energooszczędny i mniej szkodliwy dla środowiska. Innowacyjne podejście obejmuje także wykorzystanie nanotechnologii do produkcji membran o wysokiej selektywności, co umożliwia jeszcze dokładniejszą separację składników. Kolejnym trendem jest automatyzacja procesów destylacyjnych, która pozwala na precyzyjne monitorowanie i kontrolowanie wszystkich parametrów pracy urządzenia w czasie rzeczywistym. Dzięki systemom informatycznym można szybko reagować na zmiany warunków operacyjnych oraz optymalizować procesy w celu osiągnięcia jak najlepszych wyników. Warto również wspomnieć o zastosowaniu sztucznej inteligencji w analizie danych procesowych, co pozwala na przewidywanie potencjalnych problemów oraz optymalizację pracy destylatorów.
Jakie są koszty eksploatacji destylatora przemysłowego
Koszty eksploatacji destylatora przemysłowego są kluczowym czynnikiem wpływającym na opłacalność całego procesu produkcyjnego. Wśród głównych kosztów można wymienić wydatki związane z energią, surowcami oraz konserwacją urządzeń. Koszty energii mogą stanowić znaczną część całkowitych wydatków, zwłaszcza w przypadku dużych zakładów produkcyjnych, gdzie procesy podgrzewania i chłodzenia są intensywne. Dlatego wiele firm inwestuje w technologie zwiększające efektywność energetyczną, takie jak odzysk ciepła czy zastosowanie odnawialnych źródeł energii. Koszty surowców również mają duże znaczenie; wybór odpowiednich materiałów oraz ich jakość wpływa na efektywność procesu oraz jakość końcowych produktów. Regularna konserwacja destylatorów jest niezbędna do utrzymania ich sprawności i zapobiegania awariom, co wiąże się z dodatkowymi kosztami dla przedsiębiorstw.
Jakie są przyszłe kierunki rozwoju technologii destylacji przemysłowej
Przyszłość technologii destylacji przemysłowej zapowiada się obiecująco dzięki ciągłemu rozwojowi innowacyjnych rozwiązań oraz rosnącej świadomości ekologicznej w przemyśle. Jednym z kluczowych kierunków rozwoju jest dalsza automatyzacja procesów produkcyjnych, która pozwoli na zwiększenie efektywności i redukcję kosztów operacyjnych. Systemy oparte na sztucznej inteligencji będą coraz częściej wykorzystywane do analizy danych procesowych, co umożliwi optymalizację warunków pracy destylatorów oraz szybsze reagowanie na ewentualne problemy. Również rozwój technologii odzysku ciepła stanie się istotnym elementem strategii mających na celu zwiększenie efektywności energetycznej procesów destylacyjnych. W miarę rosnącej presji ze strony regulacji środowiskowych, przedsiębiorstwa będą musiały inwestować w technologie minimalizujące negatywny wpływ produkcji na środowisko, takie jak systemy filtracji czy oczyszczania gazów odlotowych. Ponadto rozwój materiałów o wysokiej odporności chemicznej i termicznej umożliwi budowę bardziej trwałych i wydajnych urządzeń destylacyjnych.
Jakie są kluczowe aspekty bezpieczeństwa przy pracy z destylatorami przemysłowymi
Bezpieczeństwo pracy z destylatorami przemysłowymi jest niezwykle istotnym zagadnieniem, które powinno być priorytetem dla każdego zakładu produkcyjnego. Kluczowym aspektem jest zapewnienie odpowiednich warunków pracy dla operatorów urządzeń; należy zadbać o to, aby pracownicy byli dobrze przeszkoleni w zakresie obsługi sprzętu oraz procedur awaryjnych. Ważne jest również regularne przeprowadzanie inspekcji technicznych oraz konserwacji urządzeń, aby zapobiegać awariom mogącym prowadzić do wycieków substancji chemicznych lub pożarów. Kolejnym istotnym elementem jest monitorowanie warunków pracy w obrębie zakładu; odpowiednie systemy detekcji gazu mogą pomóc w szybkim wykrywaniu potencjalnie niebezpiecznych sytuacji. Należy także stosować odpowiednie środki ochrony osobistej dla pracowników, takie jak odzież ochronna czy maski przeciwgazowe, aby minimalizować ryzyko narażenia na działanie szkodliwych substancji chemicznych.
Jakie są korzyści z zastosowania destylatorów przemysłowych
Wykorzystanie destylatorów przemysłowych przynosi wiele korzyści, które mają kluczowe znaczenie dla efektywności procesów produkcyjnych w różnych branżach. Przede wszystkim, destylacja pozwala na uzyskanie wysokiej czystości produktów, co jest niezwykle istotne w takich sektorach jak farmacja czy przemysł spożywczy. Dzięki temu możliwe jest spełnienie rygorystycznych norm jakościowych oraz regulacji prawnych. Kolejną zaletą jest możliwość separacji składników o różnych temperaturach wrzenia, co umożliwia efektywne wykorzystanie surowców i minimalizację strat. Destylatory przemysłowe są również elastyczne i mogą być dostosowywane do różnych procesów technologicznych, co pozwala na ich szerokie zastosowanie w różnych branżach. Dodatkowo, nowoczesne technologie stosowane w destylacji przyczyniają się do zwiększenia efektywności energetycznej, co przekłada się na niższe koszty operacyjne i mniejszy wpływ na środowisko.