Destylacja rozpuszczalników to proces, który polega na oddzieleniu składników mieszaniny na podstawie różnicy ich temperatur wrzenia. Jest to jedna z najstarszych metod separacji substancji chemicznych, która znajduje zastosowanie w różnych dziedzinach, od przemysłu chemicznego po laboratoria badawcze. Proces ten zazwyczaj rozpoczyna się od podgrzewania cieczy, co powoduje, że składniki o niższej temperaturze wrzenia przechodzą w stan gazowy. Następnie para jest schładzana, co prowadzi do jej skroplenia i zbierania jako oddzielnego produktu. W przypadku destylacji rozpuszczalników kluczowe jest, aby wybrać odpowiednią temperaturę oraz ciśnienie, aby uzyskać jak najwyższą czystość końcowego produktu. W praktyce często stosuje się różne techniki destylacji, takie jak destylacja prosta, frakcyjna czy też destylacja pod ciśnieniem atmosferycznym lub w próżni. Każda z tych metod ma swoje zalety i ograniczenia, które należy wziąć pod uwagę przy wyborze odpowiedniego procesu dla konkretnej aplikacji.
Jakie są zastosowania destylacji rozpuszczalników w przemyśle
Destylacja rozpuszczalników ma szerokie zastosowanie w przemyśle chemicznym oraz farmaceutycznym, gdzie jest wykorzystywana do oczyszczania i separacji różnych substancji chemicznych. W przemyśle petrochemicznym proces ten jest kluczowy dla produkcji paliw oraz innych produktów naftowych. Dzięki destylacji można skutecznie oddzielić frakcje ropy naftowej, co pozwala na uzyskanie benzyny, oleju napędowego czy asfaltu. W branży farmaceutycznej destylacja jest niezbędna do oczyszczania substancji czynnych oraz rozpuszczalników używanych w produkcji leków. Oprócz tego, proces ten znajduje zastosowanie w produkcji alkoholi, gdzie destylacja służy do uzyskiwania wysokoprocentowych napojów alkoholowych z fermentowanych surowców. W laboratoriach badawczych destylacja jest często wykorzystywana do analizy chemicznej oraz przygotowywania czystych reagentów.
Jakie są różnice między destylacją prostą a frakcyjną
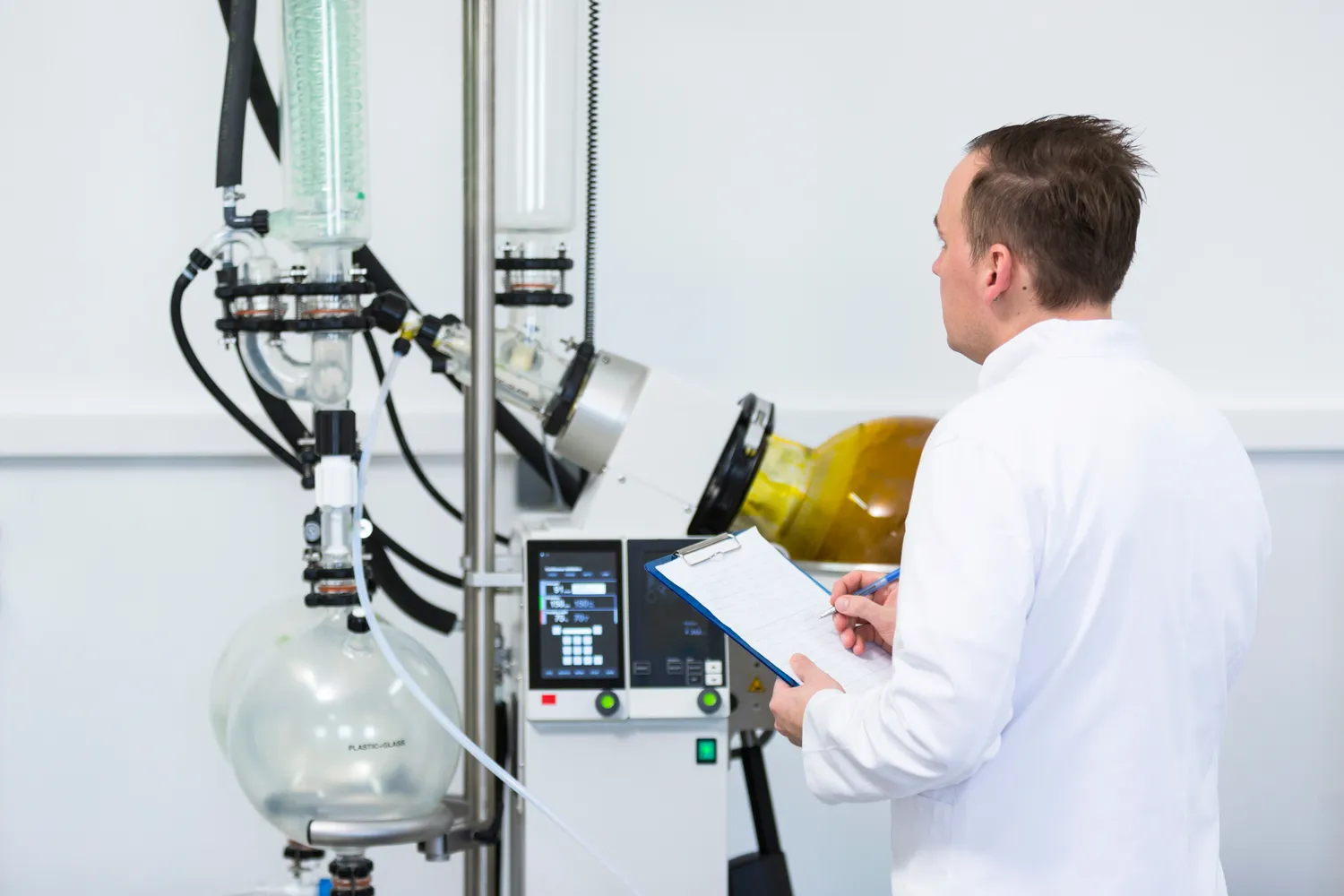
Destylacja prosta i frakcyjna to dwie podstawowe metody stosowane w procesie separacji składników mieszanin cieczy na podstawie różnicy ich temperatur wrzenia. Destylacja prosta jest najprostszą formą tego procesu i polega na podgrzewaniu cieczy do momentu, gdy jeden ze składników zaczyna parować. Para ta następnie przechodzi przez chłodnicę, gdzie skrapla się i zbiera jako produkt końcowy. Metoda ta jest skuteczna jedynie w przypadku mieszanin zawierających składniki o znacznej różnicy temperatur wrzenia. Z kolei destylacja frakcyjna jest bardziej zaawansowaną techniką, która pozwala na oddzielanie składników o zbliżonych temperaturach wrzenia poprzez zastosowanie kolumny frakcyjnej. Kolumna ta umożliwia wielokrotne kondensowanie i parowanie składników, co prowadzi do ich lepszego rozdzielenia. Dzięki temu destylacja frakcyjna jest bardziej efektywna w przypadku skomplikowanych mieszanin chemicznych, takich jak ropa naftowa czy mieszanki alkoholi.
Jakie są najważniejsze czynniki wpływające na efektywność destylacji
Efektywność procesu destylacji rozpuszczalników zależy od wielu czynników, które mogą wpływać na jakość i ilość uzyskanego produktu końcowego. Jednym z kluczowych elementów jest temperatura wrzenia poszczególnych składników mieszaniny. Im większa różnica między temperaturami wrzenia, tym łatwiejsze będzie ich oddzielenie podczas procesu destylacji. Kolejnym istotnym czynnikiem jest ciśnienie atmosferyczne; obniżenie ciśnienia może prowadzić do zmniejszenia temperatury wrzenia substancji, co ułatwia separację składników lotnych. Ważną rolę odgrywa również konstrukcja aparatury destylacyjnej; kolumny frakcyjne oraz chłodnice muszą być odpowiednio zaprojektowane i dostosowane do specyfiki procesu, aby zapewnić maksymalną efektywność separacji. Dodatkowo czas trwania procesu oraz intensywność podgrzewania mają znaczenie dla uzyskania optymalnych wyników; zbyt szybkie podgrzewanie może prowadzić do niepożądanych reakcji chemicznych lub degradacji składników.
Jakie są najczęstsze błędy w procesie destylacji rozpuszczalników
W procesie destylacji rozpuszczalników mogą wystąpić różne błędy, które wpływają na jakość i wydajność uzyskiwanych produktów. Jednym z najczęstszych problemów jest niewłaściwe ustawienie temperatury podgrzewania. Zbyt wysoka temperatura może prowadzić do nadmiernego parowania i utraty cennych składników, podczas gdy zbyt niska temperatura może skutkować nieefektywnym oddzieleniem substancji. Kolejnym błędem jest niewłaściwe dobranie aparatury destylacyjnej; użycie kolumny frakcyjnej o niewłaściwych parametrach może prowadzić do nieefektywnego rozdzielenia składników. Warto również zwrócić uwagę na czystość używanych materiałów; zanieczyszczenia mogą wpływać na wyniki destylacji, prowadząc do uzyskania produktów o niższej jakości. Inny częsty błąd to brak odpowiedniej kontroli ciśnienia w systemie; zmiany ciśnienia mogą znacząco wpłynąć na temperatury wrzenia składników, co z kolei wpływa na efektywność procesu. Dodatkowo, nieuwzględnienie czasu trwania destylacji oraz niewłaściwe zarządzanie chłodzeniem pary mogą prowadzić do nieoptymalnych wyników.
Jakie są nowoczesne technologie w destylacji rozpuszczalników
W ostatnich latach nastąpił znaczny rozwój technologii związanych z destylacją rozpuszczalników, co przyczyniło się do zwiększenia efektywności i jakości tego procesu. Nowoczesne systemy destylacyjne często wykorzystują zaawansowane technologie, takie jak destylacja membranowa czy też techniki wykorzystujące ultradźwięki. Destylacja membranowa polega na separacji składników mieszaniny za pomocą specjalnych membran, które pozwalają na przechodzenie tylko wybranych substancji. Ta metoda jest szczególnie przydatna w przypadku mieszanin o złożonym składzie chemicznym, gdzie tradycyjne metody destylacji mogą być mniej efektywne. Techniki ultradźwiękowe natomiast wykorzystują fale dźwiękowe do zwiększenia efektywności procesu separacji, co pozwala na szybsze i bardziej dokładne oddzielanie składników. Dodatkowo, automatyzacja procesów destylacyjnych staje się coraz bardziej powszechna; nowoczesne systemy monitorowania i kontroli pozwalają na precyzyjne zarządzanie parametrami procesu, co przekłada się na lepszą jakość produktów końcowych.
Jakie są różnice między destylacją a innymi metodami separacji
Destylacja jest jedną z wielu metod separacji składników mieszanin cieczy, ale wyróżnia się ona kilkoma istotnymi cechami w porównaniu do innych technik, takich jak ekstrakcja czy chromatografia. Podstawową różnicą jest to, że destylacja opiera się na różnicy temperatur wrzenia składników, podczas gdy ekstrakcja polega na wykorzystaniu rozpuszczalnika do wydobycia pożądanych substancji z mieszaniny. Ekstrakcja może być bardziej efektywna w przypadku substancji o podobnych temperaturach wrzenia lub w sytuacjach, gdy konieczne jest oddzielenie składników o niskiej lotności. Z kolei chromatografia to technika separacji oparta na różnicy w powinowactwie składników do fazy stacjonarnej i ruchomej; jest to metoda bardziej skomplikowana i czasochłonna, ale umożliwia uzyskanie bardzo czystych produktów końcowych. W kontekście przemysłowym destylacja często jest preferowaną metodą ze względu na swoją prostotę i efektywność w przypadku dużych ilości materiału.
Jakie są kluczowe aspekty bezpieczeństwa podczas destylacji
Bezpieczeństwo podczas procesu destylacji rozpuszczalników jest niezwykle istotne, ponieważ wiele używanych substancji chemicznych może być łatwopalnych lub toksycznych. Kluczowym aspektem bezpieczeństwa jest odpowiednie zabezpieczenie aparatury przed ewentualnymi wyciekami czy eksplozjami. Należy zadbać o to, aby wszystkie połączenia były szczelne oraz aby system był wyposażony w odpowiednie zawory bezpieczeństwa. Użycie materiałów odpornych na wysokie temperatury oraz ciśnienie jest również kluczowe dla zapewnienia bezpieczeństwa operacji. Kolejnym ważnym elementem jest wentylacja pomieszczeń, w których odbywa się proces destylacji; zapewnienie odpowiedniego przepływu powietrza minimalizuje ryzyko gromadzenia się szkodliwych oparów. Pracownicy powinni być przeszkoleni w zakresie obsługi aparatury oraz znajomości procedur awaryjnych; noszenie odpowiednich środków ochrony osobistej, takich jak rękawice czy okulary ochronne, jest również niezbędne.
Jakie są przyszłe kierunki badań nad destylacją rozpuszczalników
Przyszłość badań nad destylacją rozpuszczalników koncentruje się na kilku kluczowych obszarach mających na celu zwiększenie efektywności i ekologiczności tego procesu. Jednym z głównych kierunków jest rozwój nowych materiałów dla kolumn frakcyjnych oraz chłodnic, które mogłyby poprawić wydajność separacji oraz zmniejszyć zużycie energii. Badania nad zastosowaniem nanotechnologii w konstrukcji membran do destylacji membranowej również stają się coraz bardziej popularne; materiały te mogą znacząco zwiększyć efektywność separacji poprzez poprawę selektywności i przepuszczalności membran. Inny obszar badań dotyczy integracji procesów chemicznych z procesami separacyjnymi; połączenie reakcji chemicznych z destylacją może prowadzić do oszczędności czasu i zasobów oraz zwiększenia wydajności produkcji. Ponadto rośnie zainteresowanie technologiami przyjaznymi dla środowiska; badania nad wykorzystaniem odnawialnych źródeł energii do podgrzewania cieczy w procesie destylacji mogą przyczynić się do zmniejszenia śladu węglowego tej technologii.